An engagement study listed the following as recommendations for manufacturing employee retention and frontline empowerment:
- Increase frontline involvement to empower workers,
- Give your frontline teams a voice in decision-making
- Encourage your frontline to work together to improve your organization
Adopting a continuous improvement mindset will allow for a proactive approach to frontline empowerment and engagement. In this two-part blog series, Raven COO, Dr. Paul Turner, VP of Operations, Brenda Munyukwi and DuraVent Group Production Manager, Mike Gardner discuss how leading manufacturers drive frontline employee engagement through ownership on the floor, the three dimensions to boost frontline empowerment, and the frontline’s impact on productivity improvements.
Driving frontline employee engagement through ownership on the floor
When operators on the lines are empowered to provide high value with minimal effort, it makes their day-to-day responsibilities easier. Imagine an operator attending to a dozen or more machines that are going down 10-15 times a day. Expecting that operator to label specific downtimes on each instance is a recipe for disengagement. This challenge was tackled using digital OEE improvement technology. Operators can see how close they are to hitting targets, how their teammate next to them is doing, and how they’re doing as a team overall.
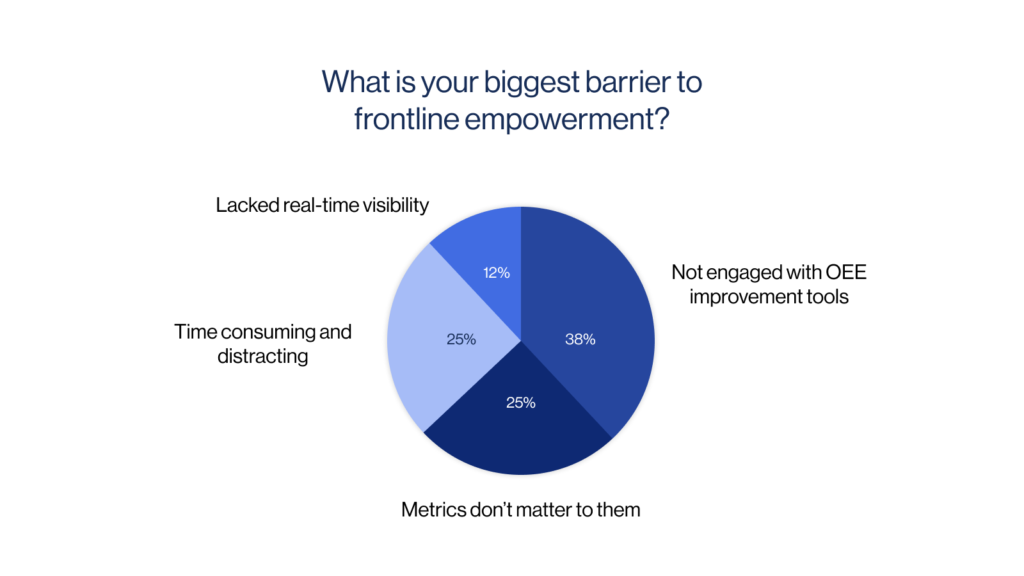
Traditionally, DuraVent had paper records that were reviewed the next day or end of shift. “We can’t have an impact, learn or maneuver on lost production time. With Raven’s smart assistants, we instantly support the operator with any issues on the lines. This quick access to data that matters to them helped them feel comfortable with new technology and gain trust. By moving to a digital format with common ‘shop’ talk, it was easier for the team to communicate. This meant improved data accuracy, faster reporting, and happier operators and supervisors,” noted Mike Gardner, Production Manager at DuraVent.
On top of smart assistants, having data on display using real-time analytics dashboards and leaderboards created a collaborative culture to increase productivity. DuraVent had many long-time operators who were awesome at their job — but weren’t always engaged. With manufacturing dashboards, operators began approaching management and having two-way conversations around goals and KPIs (that maybe they were previously unaware of). Valuable chats like these were important to drive continuous OEE improvements across the organization.
The three dimensions to empowering the frontline
The three dimensions of empowerment tie into creating an exceptional operator experience — something we strive for at Raven. We work to remove the burden of generating highly granular and accurate event timelines. This is the route to gathering, trust, engagement, and ultimately, successful digital transformation on the factory floor. Here are some considerations for frontline empowerment:
Make it easy
If you need the operator to record downtime reasons, it has to be as easy as possible for them. Take into consideration that operators are often wearing gloves in environments that can make this challenging. Operators don’t want to walk away from their stations or remove protective coverings to tag downtime. A touch of a button captures important human context often missed when using manual processes or other digital platforms.
Automate it
To relieve operator burden, automate as much of the tagging as possible. The more tagging that’s automated, the less distracted the operator is. For example, while an operator is trying to stabilize a machine after changeover, stopping to tag downtime could be unsafe or inconvenient.
Provide utility
The operator needs to feel that tagging the downtime is useful to their communication process. For example, if a machine runs out of raw materials and stops producing, instant alerts and notifications can let the materials handling department know the issue, assigning the team’s responsibility. This process gives the operator an opportunity to communicate that they aren’t the source of the downtime.
The frontline’s impact on shop floor improvements with Raven
A frontline team that has the tools and support to focus on their job will have a positive impact reaching beyond their workstation. By using a digital solution like Raven, operators are engaged in data collection and decision-making processes. By the end of their day, the frontline knows they’re valued and are empowered to continue making important contributions on the shop floor every shift.
A new perspective on time
Once DuraVent began working with Raven, the team could react to issues within minutes or even seconds. DuraVent has cap times and cycle times on products that are 10 to 15 seconds. Every 10 to 15 seconds, parts are coming out and going in the box to ship out, so hours and minutes really matter. “Having the ability to say, “Hey, I have an issue, and I need you here within one minute or it’s going to impact 10 to six parts” absolutely changed everything,” said Mike Gardner, Production Manager, DuraVent Group.
DuraVent’s downtime dramatically decreased and production output increased. With people being the most important asset, Raven’s technology really changed the relationship they had with their operators. Frontline teams were no longer asked to recall what happened 24 hours ago. Operators and management were quickly able to see what issues arose and resolved them fast — before losing minutes, hours or days.
Accurate, complete data anywhere
Supervisors and team leads are now able to see the same real-time production information in their office and tablets on the shop floor. At a glance, they have access to a visual status of production and business targets that eliminate the need to interrupt operators.
Teams can look at their screens and see every single machine that Raven’s tied to. Operators can see what the standard, expected and current rates are, whether they’re ahead or behind, or just there in the nick of time.
Efficient changeovers with real-time visibility into scheduling
Once the data was front and center, DuraVent was amazed to discover that their biggest losses were on three items. At that point, the team changed their production schedule to help mitigate those losses. After making the changeover modifications, they saw vast improvements in output, efficiency and utilization.
No hidden losses with automation
With downtime tracking through automation and operator input, accurate and granular labeling of minor micro-stops is possible. Companies who are labeling up to 100% of downtime are able to gain actionable insights that can drive continuous OEE improvement decisions when they probably wouldn’t have even bothered before.
When operators are empowered to take ownership of collecting accurate, actionable data. This provides a visual event timeline used as a collaborative, common language with factory management to make effective process adjustments.
When introducing improved processes on the shop floor using OEE technologies, it’s critical to include the voice of operators on the frontline to help make operational improvements. DuraVent did so using quick and easy downtime tracking for the frontline, resolving issues on the fly and significantly increasing throughput as a collaborative team.
Need help with tech buy-in that empowers your frontline to drive results?
Get your Starter Kit that includes 3+ free resources to help you make the pitch to switch from manual, time-consuming processes to quick, automated processes at your factory.