Improve changeover efficiency, increase production speed and guide frontline action — all in one place.
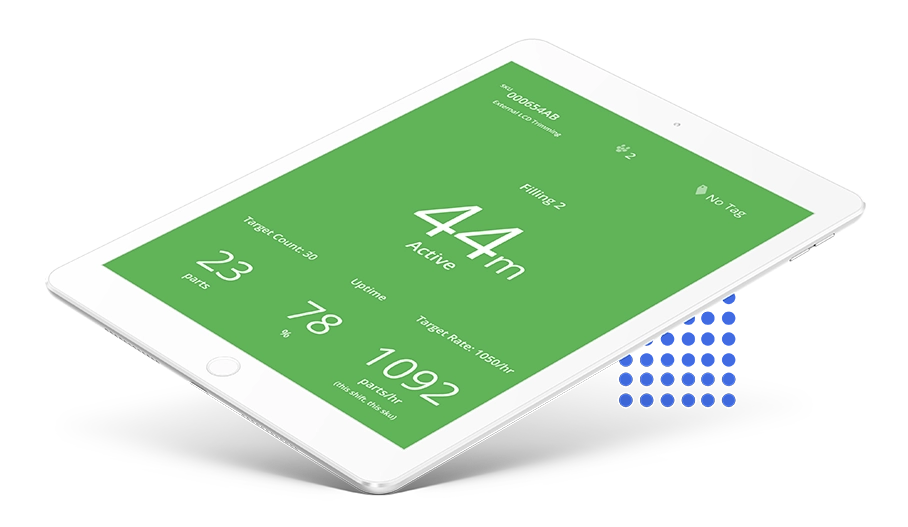
Trusted by leading manufacturers worldwide:
Transform shop floor operations for increased productivity and a happy frontline
Your frontline is your most valuable resource, playing a crucial role in the operations and sustainability of your plant. Equip them with the tools they need to succeed.
Engage your frontline teams by giving them 100% real-time visibility into the metrics that matter to them and guidance on how to win each shift, using Raven’s downtime tracking software.
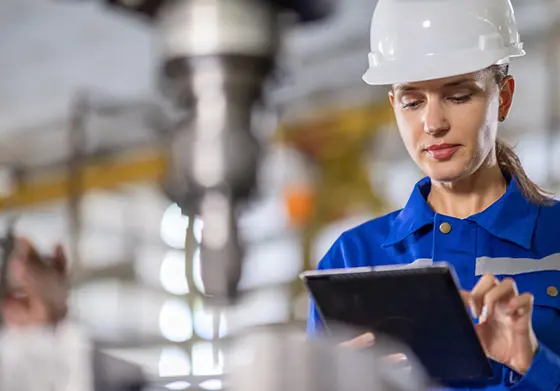
Frontline-Friendly Features
Downtime tracking software powered by machine data and human context
Capturing operator context is critical to understanding what’s really happening on the shop floor. With an intuitive HMI on their lines, operators are engaged to provide meaningful context. With or without greasy gloves, context is captured quickly and operator burden is reduced by 10x.
Learn More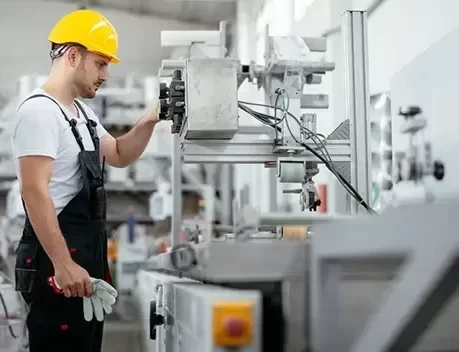
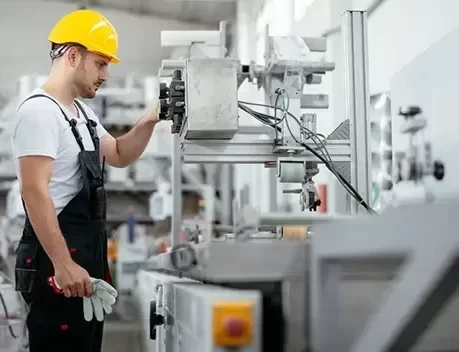
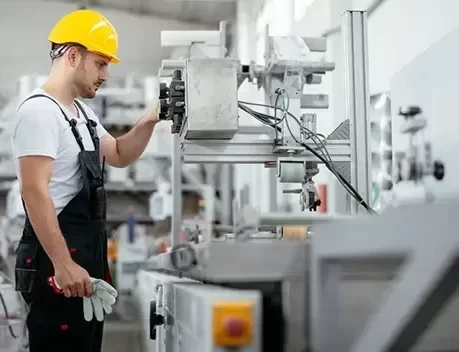
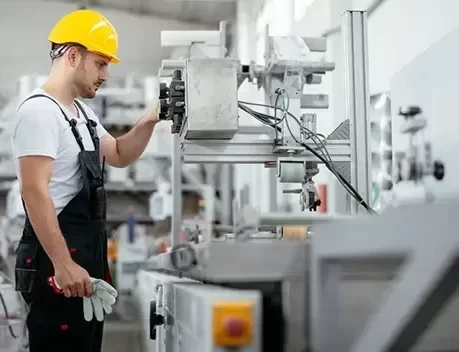
Customer Wins
ECCO Manufacturing uncovered hidden capacity to produce more
Learn how ECCO drastically reduced operator burden and achieved strong engagement with a 95%+ downtime tagging rate in just 3 months.
Management Features
Empower supervisors and shift leads to guide improvements
Do you know when your machines are running and when they’re not? If they’re running, are they performing the way they should? Without a digital downtime tracker solution, it’s not an easy question to answer.
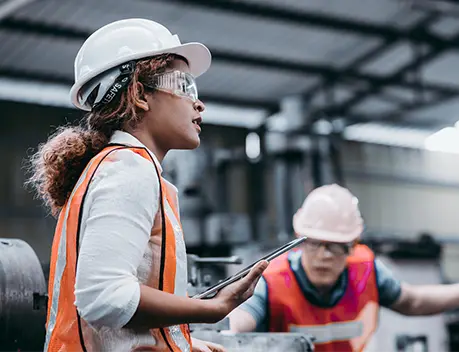
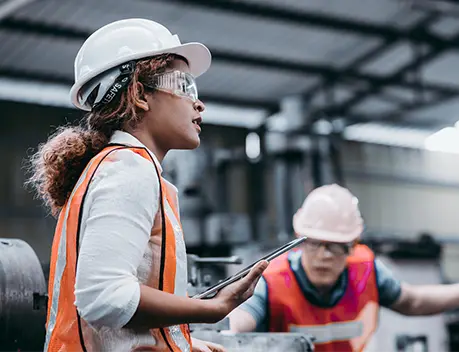
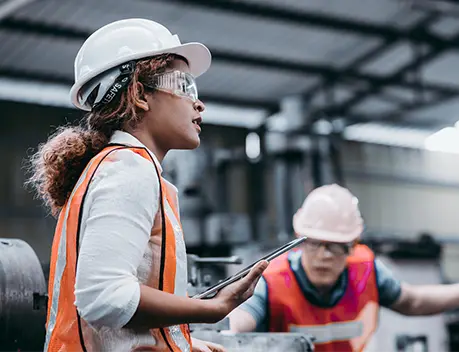
Fuel friendly competition using gamification
Companies with highly engaged workers tend to outperform those without by 202% (Gallup). With a real-time glance into their productivity on digital displays and end-of-line dashboards, your frontline knows when they’re winning or losing – igniting motivation to hit targets.
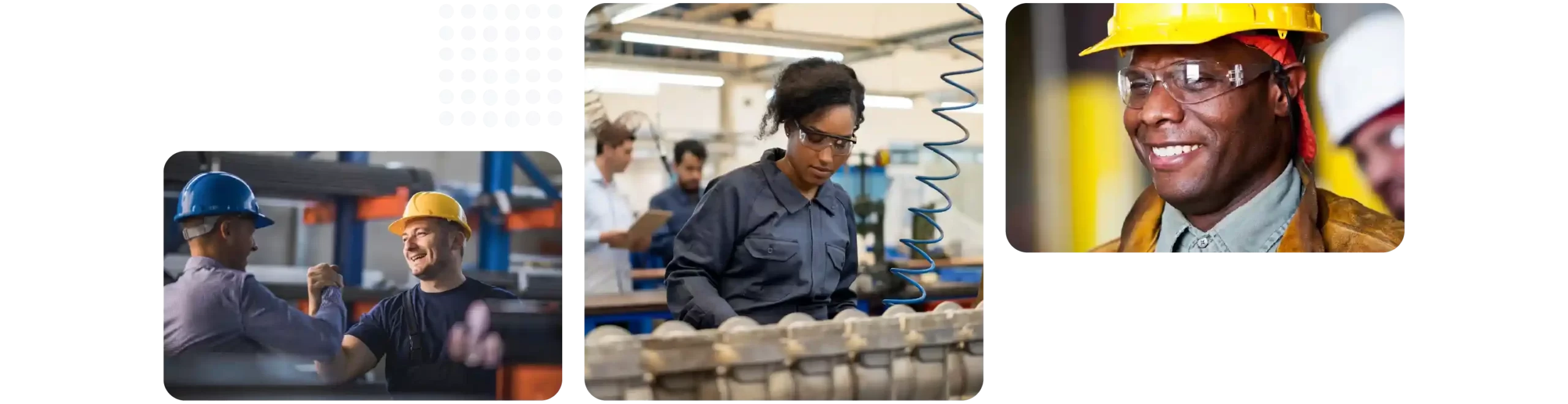
The connected worker: Attract and retain the curious
If asked to choose between a connected job or an unconnected one, odds are you’d choose connected. You don’t even need to know much about what “connected worker” means in practice to decide that it sounds neat.
By implementing new tools and technology, like downtime tracking software, that are purpose-built for the shop floor, you’ll attract an agile, innovative workforce that wants to be involved in digital adoption and decision-making to drive productivity improvements. Fresh perspectives will power more manufacturing wins.
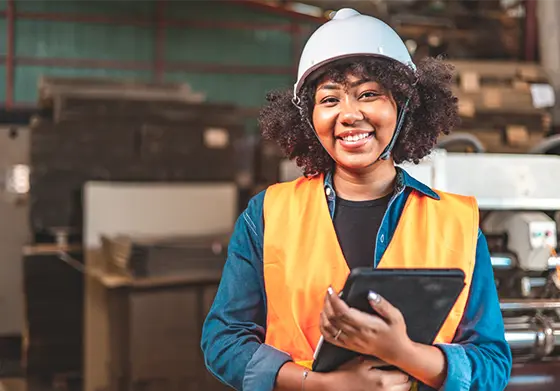
Put your people first, celebrate more wins
Learn how Raven can help you get 100% visibility into shop floor operations and make sustainable improvements.